GUARANTEED PRECISION WHEN EVERYTHING MATTERS
ADVANCED TOOLHOLDING FOR THE
AEROSPACE INDUSTRY
Whether machining high-precision components for commercial, defense or space applications, aerospace manufacturers face similar production challenges. Getting the most from their tools while reducing scrap and costs are all priorities when processing tight-tolerance parts from unique and challenging materials. In aerospace production, everything matters.
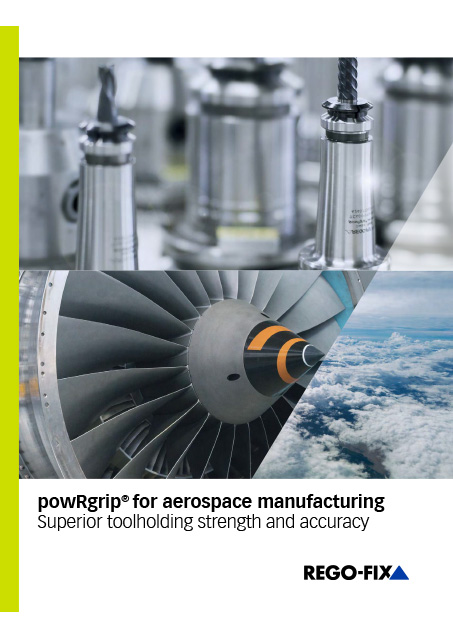
Common Challenges Faced in the Aerospace Industry
In addition to optimizing processes for consistency and repeatability, increasing tool life and output to reduce cost per part and shortening cycle times for better output, every sector of aerospace manufacturing presents unique tooling issues to master.
Commercial
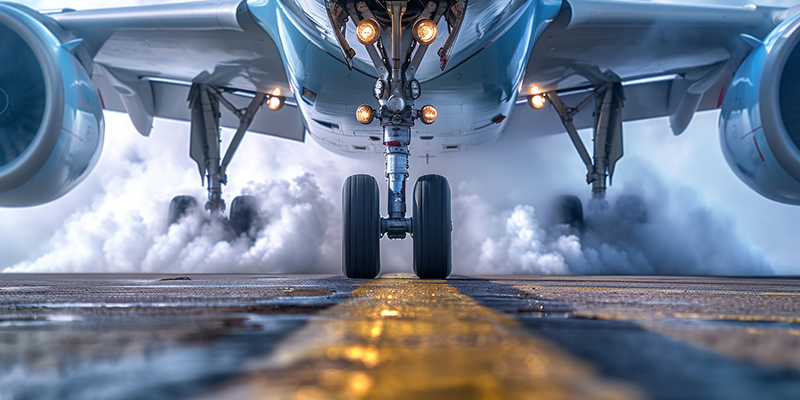
- Extended composite wing skin for improved fuel efficiency
- Minimize chatter
- Use standard tools for specialized processes
Defense
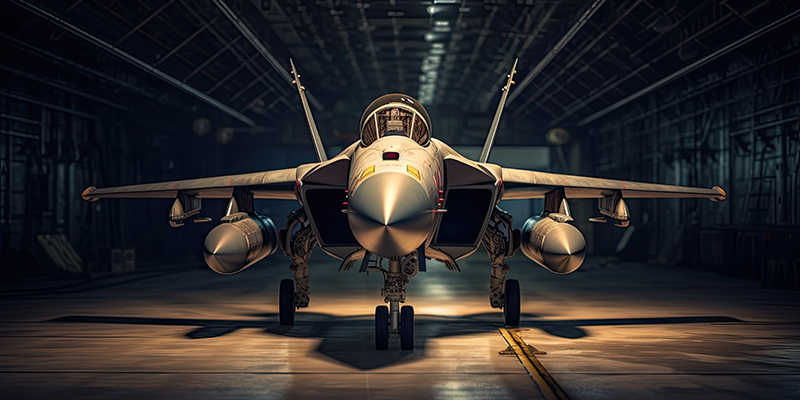
- Material stack ups & splicing
- Prevent tool pullout
- Eliminate runout
Space
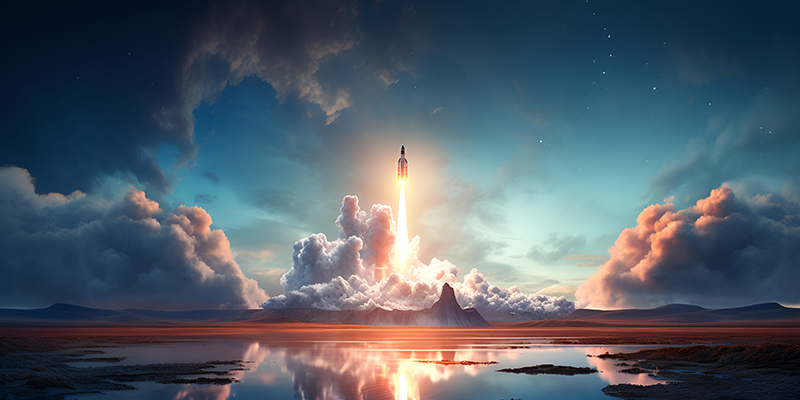
- Long-overhang tool applications
- Tight-tolerance parts with complex geometries
- Unique & challenging materials
REGO-FIX Solutions:
Run the best and most advanced toolholders ever made.
Speak to a product specialist to solve your aerospace challenges.
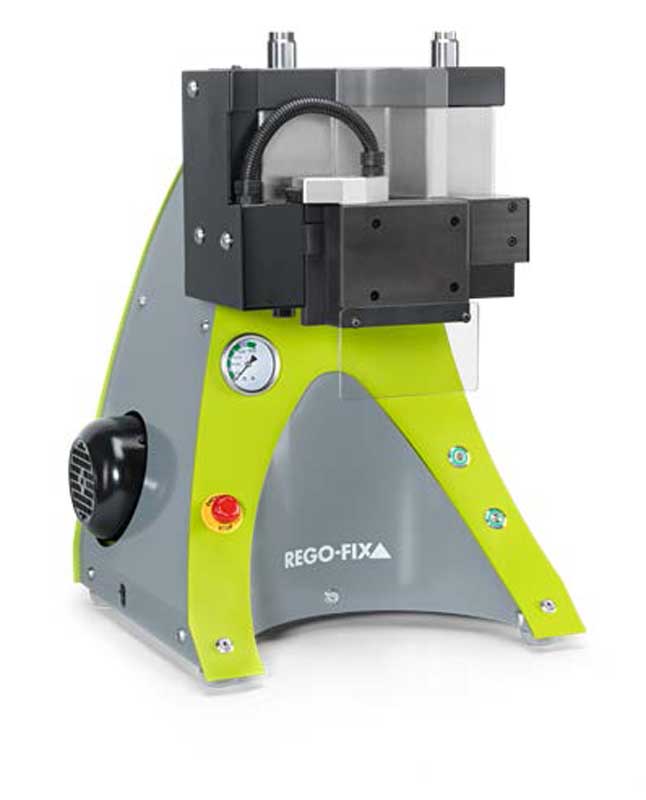
powRgrip
- Excellent vibration damping for improved tool life & surface finishes
- Total Indicated Runout (TIR) — 3 µm
- Tool changeouts 10 seconds for reduced cycle & setup times
- Tackles longreach applications & tool overhangs from 6” to 12”
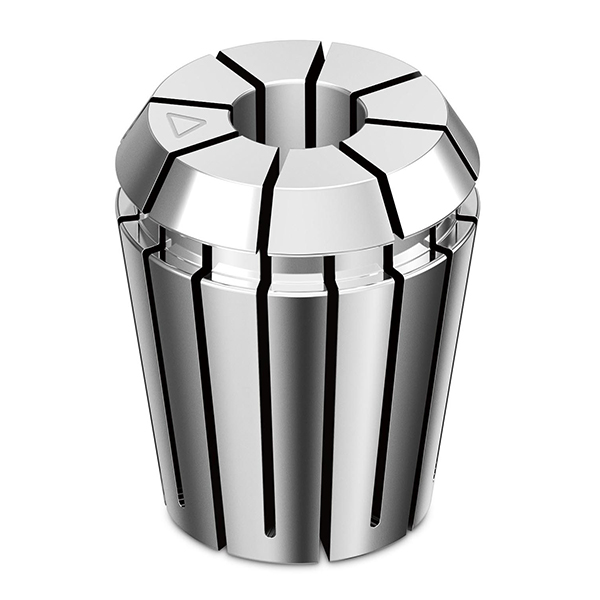
REGO-FIX ER
- Total Indicated Runout (TIR) – 10 Standard Precision; 5 µm Ultra Precision
- Product range from 0.008″ – 1.417″
- Full lot traceability for maximum process control
- 100% precision balanced for high rpm ratings
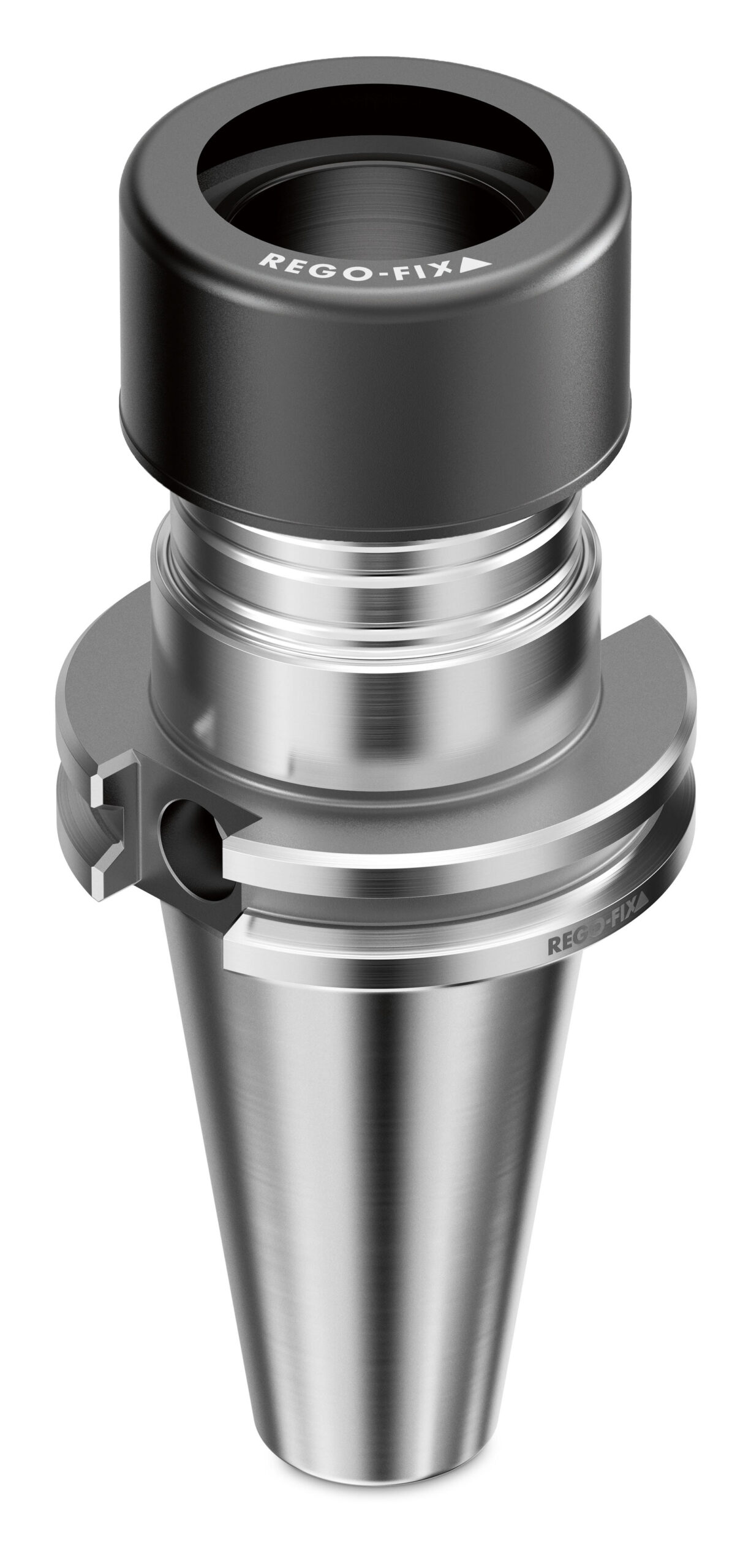
secuRgrip for powRgrip
- 100% pullout protection
- PG size 15 – 32
- Maximum security during heavy machining
- For all tools with a Weldon flat
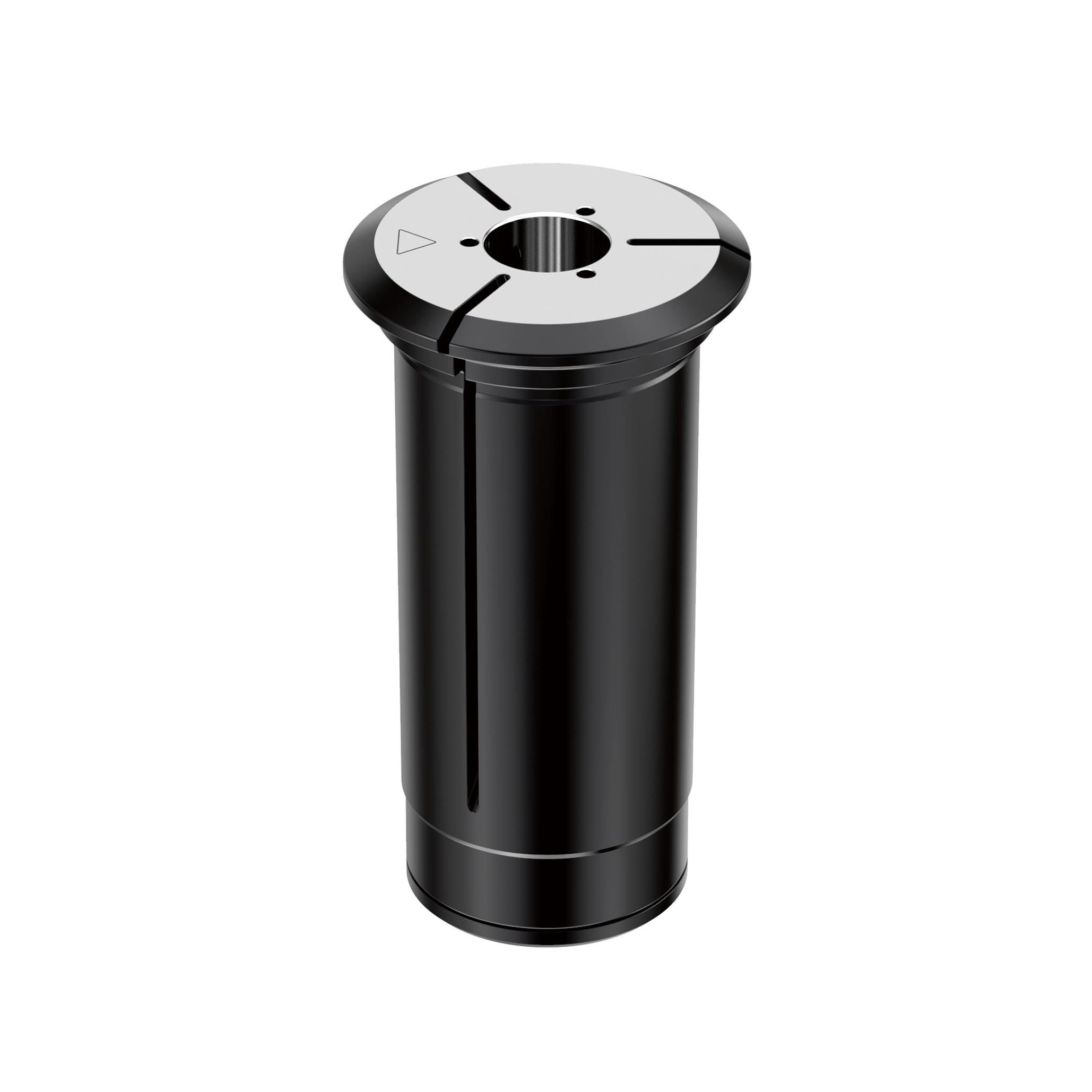
PG CoolBore Collets
- Highest clamping forces with peripheral coolant
- Total system runout – 3 µm
- PG size 25 – 32
- Shank diameter range – 6 – 20